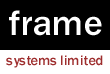 |
|
|
 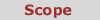 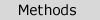 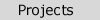 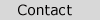 |
|
|
|
|
|
|
|
|
|
|
|
|
|
|
|
|
....
scope of activities
|
|
|
|
|
|
|
|
|
|
|
|
|
|
|
|
|
|
|
|
|
|
|
|
|
|
|
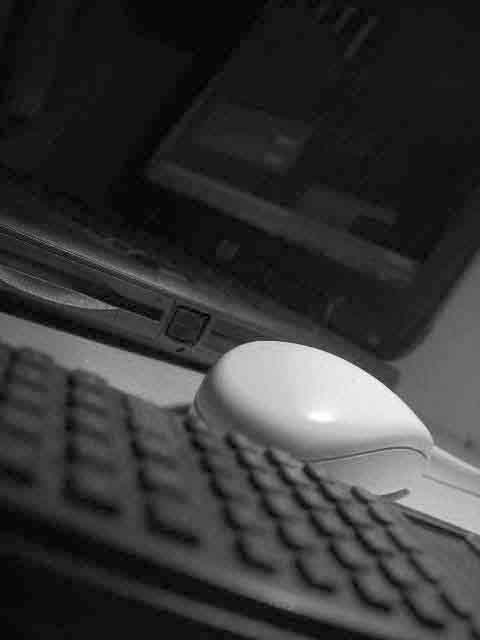 |
|
Every project or product development
presents its own challenges. Each has varying requirements, resource
demands and risks. The better these are understood at the outset the
more likely the project will be delivered on time and to budget.
Not all the phases mentioned on this
page will be important on each occasion, nor is this intended to be
a complete task set, but the following may be a useful check list to
see if key components are missing from your project.
If there are elements missing, then perhaps
we can help 'plug the gap'.
|
|
|
|
|
|
|
|
|
|
|
|
|
|
|
|
|
|
|
|
|
|
|
|
|
|
|
Marketing
and Product Management |
|
|
Designers
and engineers can be a strange bunch in that they usually do what
they are told, so it's essential that the product is well specified
at the outset. Typically, this phase would include :- |
|
|
|
|
|
|
- concept
development, features, performance, applications |
|
- requirement
analysis including review of competitive products, prices &
costs |
|
- market
research - quantitative and opinion |
|
- product,
market or business strategy development |
|
|
|
|
|
- identify
mandatory and voluntary standards and regulatory approvals |
|
|
|
|
|
|
|
|
|
|
|
|
|
|
|
|
|
|
|
|
|
|
|
|
|
|
Feasibility
Study |
|
|
Most
feasibility studies will start with a review of requirements then
progress to an initial design concept. This process helps better
to classify the potential risk areas and identify sources for key
purchased components, sub systems or IPR if they are needed. Or
the study may simply be used to refine important product features
such as a user interface or packaging design before too many expensive
commitments have been made. The scope for a study might encompass:- |
|
|
|
|
|
|
- industrial
design concepts using CAD or physical modeling |
|
|
- software
user interface mockups |
|
|
- mechanical
and electronic partitioning |
|
|
- manufacturing
routes and methods |
|
|
- concept
Bill Of Materials with unit and tooling cost forecasts |
|
|
- development
cost and timescales estimate |
|
|
|
|
|
Information
gleaned form the initial Marketing and Feasibility studies then
form part of the overall marketing plan and product(s) requirement
specifications to guide the design and development stages. |
|
|
|
|
|
|
|
|
|
|
|
|
|
|
|
|
|
|
|
|
|
|
|
|
|
Project
Planning |
|
|
|
Quite often a 'project plan' is
limited to a simply task list with timescale guestimates laid
out on a colourful chart which the Board can use as wallpaper.
For small, short duration project this is often perfectly adequate
as it at least demonstrates that someone has thought about what
needs to be done; but is it realistic, accurate and efficient
?
Accuracy is best achieved through
experience from previous activities. Efficiency is more complex.
The key function of a good plan is as a communication tool informing
all participants of their commitments, objectives and dependencies.
Efficient communication can allow project activities to run concurrently
shortening the time to market in comparison with the sequential
'relay baton' approach.
At a minimum, the plan should identify
and address:-
|
|
|
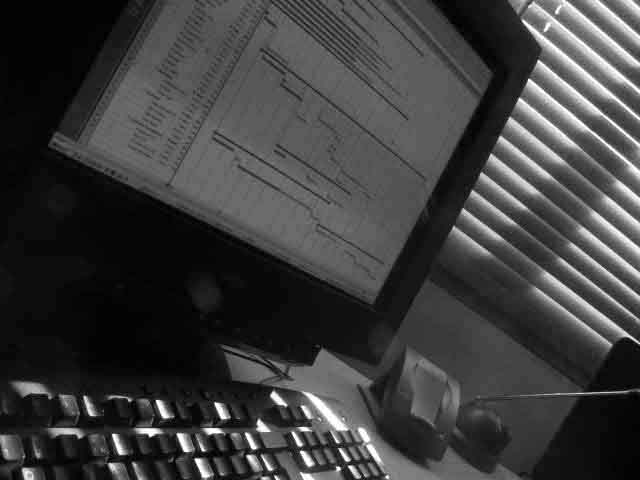 |
|
|
|
|
|
|
|
|
|
|
|
- key activities
with objectives. committed resources and planned costs |
|
|
- dependencies
between activities or tasks |
|
|
- milestones
for project reviews and expenditure release |
|
|
- risk
and unknown factors which still need to be resolved |
|
|
|
|
|
|
|
and any other details which is critical for the project to succeed.
It's arguable that one of the biggest problems with project plans
is over complexity and to be an effective tool the rule is 'keep
it simple'. |
|
|
|
|
|
|
|
|
|
|
|
|
|
|
|
|
|
|
|
|
|
|
|
Detailed
Design and Engineering |
|
With adequate preparation a detailed
design should proceed efficiently with the obvious proviso that
the correct skills and talent are available for the project. Good
design has to be elegant and maintainable. Creativity is equally
as important as employing the most applicable, techniques, devices
or tools and it's no boast to say that Frame Systems has collaborated
with some of the most talented engineers and designers in their
field.
The combined breadth of experience
is too long to detail here and it's sufficient to identify some
of the disciplines we are able to support :-
|
|
|
|
|
|
- electronic hardware
including most programmable technologies |
|
|
|
- control firmware
and real time software systems |
|
|
|
- analogue (instrumentation
through video etc) |
|
|
|
- pcb layout and mechanical
packaging |
|
|
|
- mechanical design
of machines, equipment |
|
|
|
- design of tooling
for plastic / casting etc. |
|
|
|
- documentation, including
user and technical manuals |
|
|
|
- design reviews and
appraisal |
|
|
|
|
|
|
Subject
to availability and needs, we can undertake the complete design
or dovetail into an established engineering team to augment existing
capabilities. |
|
|
|
|
|
|
|
|
|
|
|
|
|
|
|
|
|
Project
Management |
|
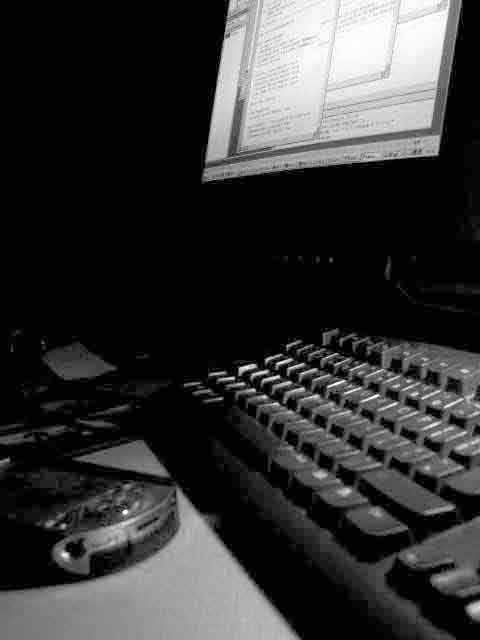 |
|
Even the best plan will soon collapse
if the project is not effectively managed and the plan updated
to cater for real events. Continuous progress monitoring through
informal or formal reviews should be maintained and the resuts
and information openly shared with all members of the project
team. As mentioned before, good communication is the key to effective
projet management. It's communication which enables clear, informed
decision making and empowers all contributors to operate effectivly
together.
Doubtless, most visitors will regard
this as just common sense, but it's remarkable how members of
some 'teams' simply don't have a clue as to what the real issues
and objectives are. Pooling resorces and ideas can enhance problem
solving and peer pressure is a great motivator. Often an 'outsider'
is able to maintain a more dispassionate perspective to a situation
and interim project management can release valuable internal resources
to execute the job in hand.
|
|
|
|
|
|
|
|
|
|
|
|
|
|
|
|
|
|
|
Production
Engineering, Introduction and Product Support |
|
Although sometimes neglected until
the last stage stages of a development, Production should be involved
right at the start. It's Production that will actually have to
deliver the product so it's a good idea to ensure they can make
it. This is equally true for both internal and subcontracted manufacturering.
Similarly for customer or product
support / service teams. Get them in early as they will have a
lot of suggestions for improvements and cost savings. Common sense
again ? Yes, but it has been woefully neglected by some in the
past.
If the gap is here, then Frame
Systems might be able to support the introduction to pilot or
full production, particularly when all manufacturing is to be
subcontracted and internal expertise is limited.
|
|
|
|
|
|
|
|
|
|
|
|
|
|
|
|
|
|
Product
Launch and Marketing |
We probably all recognise the mad
rush, sometimes leading to panic, as the launch date approaches.
Trade shows, brochures, demonstrations and sales training all
occurring at once with limited product and staff availability.
Again planning is key as is a disciplined and structured approach
to designing, organising, testing and rehearsing demonstrations
and presentations. We can't stop the clock, but we can undertake
and support a wide range of these tasks, up to and including planning
and organising the entire launch.
|
|
|
|
|
|
|
|
|
|
|
|
|
|
|
|
|
|
Documentation
- Technical, Training and User Manuals |
Saving the best to last ! Let's
be honest, very few people actually enjoy writing manuals so it
nearly always gets put off to the last moment.
Content and level of detail needed
does vary significantly depending on the product, market and sales
territories, but delays in manual production will hold up final
product shipments, and thus sales.
Accepting that the 'product' is
the entire proposition to the customer, a holistic approach to
design can not relegate the manual to the last and lowest priority
on the list. Moreover, the documentation has to be tested. Failure
to test the operating, technical or service manuals is almost
as bad as not testing the hardware or software it describes. For
the user, the 'Product' may not meet their expectations as a consequence,
and this is a dissatisfied customer at the minimum or a product
return(s) or possibly recall at worst.
|
|
|
|
|
|
|
|
|
|
|
|
|
|
|
|
|
|
|
|
|
|
|
|
|
|
|
©
Frame Systems Ltd 2002
|
|
|
|
|
|
|
|
|
|
|
|
|
|
|
|
|
|
|
|
|
|
|